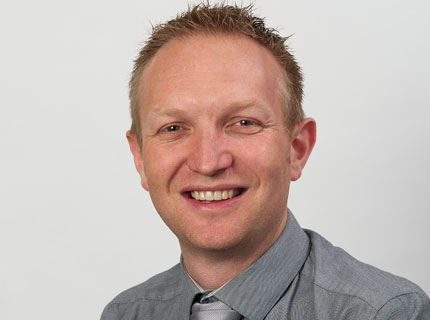
Author: Tony Tullett, Service Manager, Condair plc
The importance of expert humidifier commissioning
It is disappointing to realise that, even though humidifiers are specified for installation in most air handling systems and many process applications, many clients fail to get the best out of them because they don’t recognise the benefits of using humidification experts in the commissioning stage. But even when an expert is called in, getting them in at the wrong time can lead to problems and wasted effort by several parties later on.
When a consultant specifies a humidifier or a client asks for one to be installed, it is because it is considered an essential or desirable part of that building’s services. Despite this, little proper consideration is given to the commissioning process and a significant proportion do not function correctly as a result. Whilst lack of appropriate maintenance is the most common reason for Condair's service engineers being called to site, the many calls that come in shortly after humidifiers are first switched on indicate issues that were not appropriately addressed during commissioning.
Modern humidifiers are typically well-designed and built, with fabrication commonly being by ISO9000 accredited companies, and installation and commissioning manuals are now better written than ever before. However, given the wide range of different types of humidifier (and it’s worth listing some to make the point) – electrode-boiler, resistive steam, gas-fired, air and water atomisers, high pressure water atomisers, rotary atomisers, evaporative humidifiers, ultrasonic nebulisers, live steam injection and steam-to-steam units, many of which also involve ancillary equipment such as water treatment and compressed air systems – it is hardly surprising that few, if any, building services contractors have the expertise in-house to get the humidifier to operate as intended. This is partly because of the lack of any but the most basic information on humidifiers being part of regular H&V training and, anyway, who reads the manual?
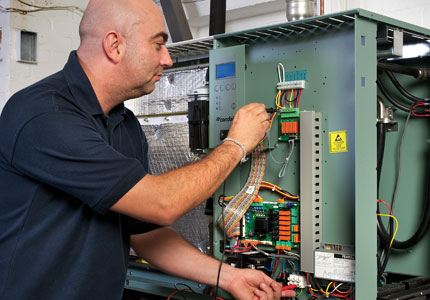
A qualified humidification engineer will be able to identify installation problems that will avoid potential problems...
A qualified humidification engineer will be able to identify installation problems that will avoid potential problems. Too many bends in steam hoses, installation of steam distribution systems immediately before obstacles, inadequate drains or water pressure, insufficient power supply and non-EMC compliant equipment next to signal cables are everyday experiences for humidifier service engineers.
Most humidification companies will ask the customer to sign a pre-visit checklist to avoid wasted journeys for basic checks like these but, even so, engineers still arrive on site to find humidifiers with no water supply or even worse, still in their packaging.
There are important matters other than the purely technical to consider. For example, the obligations outlined in the HSC’s L8 guidelines on the control of Legionnaires’ disease, means that risk assessment can be an intrinsic part of the commissioning process. A specialist is required and the manufacturer or supplier is often best placed and qualified to carry out this role.
Even when a trained humidification engineer is called in to commission a system, poor preparation and coordination on the part of the contractor mean that things can still go wrong. Despite every effort by a humidifier company's customer services department to ensure that everything is in place before an engineer goes to site, it is very common for a service engineer to arrive at a commissioning and find that the humidifier control signal is not connected or is inactive.
Seen as an easy problem to resolve, the engineer will often check with the site contact or client on whether to duplicate the signal - most service engineers carry signal generators in their toolboxes - the answer is usually "yes", and an independent control signal is then supplied. In this way, the humidifier can often be shown to be working correctly itself.
But an air handling system is an integrated whole and there is often little point in proving an individual component unless it can be also shown to work effectively in relation to all other elements. Things often go awry when the BMS or other external humidity control signal is connected later. Unsuitable signal, inappropriate interlocks and incorrect control algorithm are common problems and yet, because it is easier to see that the humidifier is not producing a suitable amount of vapour at the desired time than it is for them to understand the sophisticated interaction of all the components that make up the air handling system, the humidifier engineer is often called back to site, commonly at a time when the controls engineer isn’t there.
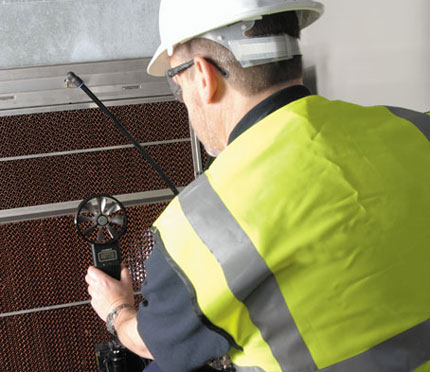
Ideally the commissioning process should involve all parties...
As a result, the humidifier and controls companies waste valuable resources going back to prove the humidifier has been installed incorrectly or risks the bad feeling that ensues, especially when insisting, quite justifiably, on payment for doing so.
It isn’t just the links between controls and humidifiers that matter. In one recent case, a 90kg/h electrode-boiler humidifier was specified where a maximum duty of 17kg/h was actually required. High ambient humidity, duct wetting and damage to the fabric and contents of the building were all blamed on the humidifier. Electrode-boiler units modulate effectively down to around 20% of output – this unit was effectively operating as an on-off unit around the bottom end of its capacity when much closer modulating control was needed. It took an experienced humidification engineer to work this out and discretely explain to the consultant, rather than cause embarrassment with the client.
It is the interaction with other systems that matters and being on site at the right time is an essential part of this. Planning and coordination is the key.
Ideally, the commissioning process should involve all parties – AHU manufacturer, the controls company, key component suppliers, contractors, the client or their nominated representative – being on site in a planned and coordinated way. The rise of specialist commissioning companies during the last 15 years has shown that the simple "switch it on and see if it works" approach is inadequate for modern, complex building services systems, and humidifiers are very much part of this.
The messages here are clear. A modern humidifier will typically do what is asked of it. However, they are complex systems, encompassing many variables that affect their performance, and they should be commissioned by experienced technicians who are present on site as part of a team working together to commission the air handling system as a whole. If this cannot happen, then organisations can generally expect to pay more for the almost inevitable return to site, to carry out what could have been achieved the first time round if the commissioning had been organised properly in the first place.