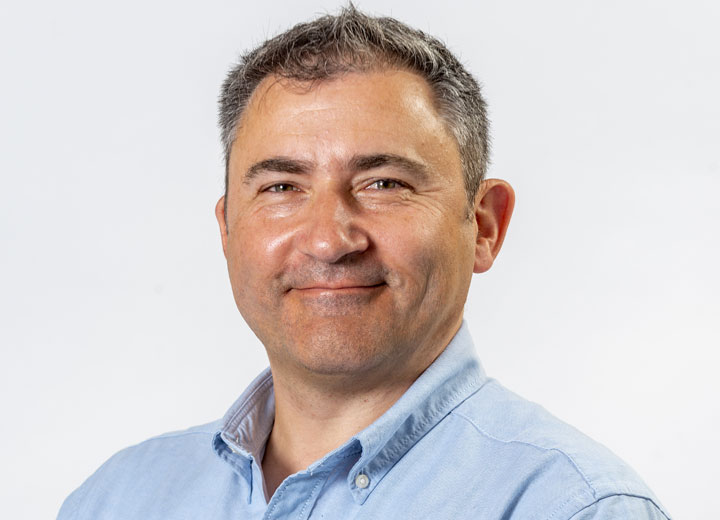
Author: Dave Marshall-George, Sales Director, Condair Limited
The energy of humidification
The use of humidifiers is essential in many different applications. From protecting valuable works of art in galleries to cooling data centres, from minimising airborne viral loads in offices to ensuring a perfectly baked crust in a bakery. Humidification is needed in many situations but worries over energy consumption are frequently the greatest concerns expressed by customers.
So how much energy is needed to humidify and what are the options for those buildings that would benefit from humidity control but also need to minimise energy use?
A humidifier turns liquid water into a gas in order to raise the air’s relative humidity to a desired level. To do this the humidifier will either boil water to create steam or evaporate cold water into the air by turning it into an aerosol or directly evaporating it from a wet surface. The energy needed in each of these scenarios is exactly the same, as determined by the laws of thermodynamics.
To change the state of 1kg of water from a liquid to a gaseous state, at normal room temperature, requires 0.68kW of energy. To extrapolate this to the needs of a typical building, an area of 1,800m³ might need 6kg/hr of additional humidity per day to maintain 45%RH during office hours. Therefore, operation during a full winter season could need approximately 11,106kg annually. Multiplying this annual requirement by the energy needed for 1kg of humidification, results in an annual energy use of 7,552kWh.
This energy comes from electricity in electrode or resistive steam humidifiers, from gas with gas-fired steam humidifiers, or mostly from the air itself in the case of cold-water humidifiers. Adiabatic humidifiers, such as spray, evaporative or ultrasonic units, still need the same 0.68kW per kg to humidify, but the energy use is relocated to a heater needed to warm the air prior to the humidifier. This is so the air can absorb moisture from the humidifier and be at an acceptable temperature after the cooling effect of evaporation from the humidifier.
So, to answer the question, how can the energy used in humidification be minimised, we really need to look at where the energy is coming from, possible efficiency improvements and whether the overall humidity load might be reduced.
Where energy is coming from is very topical at the moment with many building managers looking to decarbonise and move away from gas. Replacing gas-fired humidifiers with electric steam is currently very popular, even though the overall running costs can be higher. As electricity can be sustainably sourced, self-generating electric steam humidifiers are often seen as a greener option than gas-fired units. The same can also be true for cold water humidifiers, if they rely on gas-fired pre-heating.
Cold-water humidifiers really excel in energy use when the pre-heat comes from recovered waste heat from another process. If waste heat is available, using a heat exchanger to pre-heat the air prior to the humidifier results in a humidification system with minimal energy consumption. An evaporative humidifier can supply up to 1,200kg/h of humidity whilst itself operating on less than 1kW of electricity. If the pre-heat can be met with recovered heat, cold-water units offer exceptionally low energy humidification.
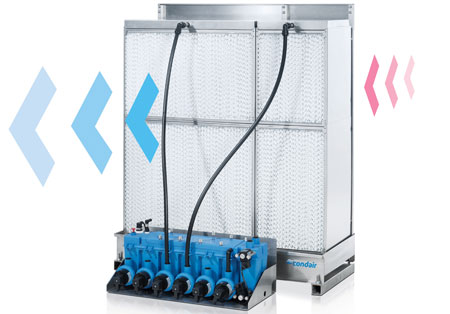
Cold-water humidifiers can also play an important role in reducing cooling energy in the summer.
Cold-water humidifiers can also play an important role in reducing cooling energy in the summer. By humidifying the warm extract airstream from a building and cooling it prior to venting, the cold humid air can be passed through a heat recovery unit to pre-cool warm incoming air. Even reducing the incoming air by just a few degrees can have significant impact on the overall cooling energy needed during the summer season.
Alongside using alternative energy sources and improving system efficiency, the third way to potentially reduce energy consumption is to look at ways to reduce the amount of humidity needed. This could be done by reviewing the hours of operation to ensure humidity levels are only being maintained as and when required. Or by using a humidifier with a more accurate level of humidity control and lowering the overall set-point. An electrode boiler will typically control to +/-10%RH, so in order to maintain humidity above 40%RH, an electrode boiler would need to be set to 50%RH. By contrast, a resistive steam humidifier run on RO water can control to +/-2%RH, so could be set to 42%RH, operating less frequently and yet still maintaining humidity above 40%RH.
Humidity recovery units are another way to potentially reduce the operating time and therefore energy use of a humidifier. These work in a similar way to heat recovery units, but rather than transfer thermal energy from one airstream to another, they transfer moisture. The humidity in outgoing exhaust air is captured in a desiccant wheel and used to humidify an incoming air stream. As these systems aren’t proactively adding moisture to the inside air, they aren’t capable of meeting a building’s total humidification needs but can be successful in reducing the humidity needed from the humidifier.
In summary, humidification does obviously need energy, just as heating or cooling does, but there are many strategies to minimise the burden. Condair can offer free on-site inspections to any building manager looking to maintain a specific humidity, whilst avoiding the headache of high energy bills.